During conversations with electric utilities, I often hear about challenges during the as-built process such as inaccurate geospatial intelligence for grid assets, laborious paper-based redlines, switching between numerous apps, and limited scanning capabilities in the field. Together, these issues lead to an enormous backlog of as-built projects.
Transform electric utility operations with accurate data and fewer field visits
To solve these challenges, IQGeo has partnered with leading North American electric utilities to develop and refine digital as-built capture best practices to help utilities boost productivity, improve data quality, and reduce trips to the field. These best practices underpin the IQGeo solution, which unifies spatial awareness, field mobility, and workflow integration to support utility operations from initial design through final as-built.
Here are the four primary ways that a well-designed geospatial solution can transform as-built processes:
-
Establish baseline capabilities
-
Integrate seamlessly with utility systems
-
Align with real-world field and office workflows
- Define the correct KPIs
1. Establish baseline capabilities
The ability to digitally record network changes accurately and efficiently is at the core of any as-built capture strategy. We’ve learned that the most effective solutions must include:
- GIS mobility. Field and office users should have access to the same GIS features and network details. This shared view ensures consistency and accuracy across teams.
- Seamless design and work management integration. Field workers need to interact with existing designs and work orders and synchronize updates back to the office.
- User-friendly interfaces. Intuitive, mobile-responsive tools make data entry faster and reduce errors. Smart forms and QR scanning streamline workflows.
- Flexible mapping tools. Teams should access base maps, geospatial data layers, and equipment details in one place, with the ability to zoom and interact with features easily.
- Configurable forms and controls. Administrators must be able to define form fields, user permissions, workflows, and symbology tailored to the utility’s network.
- Offline performance. Field tools must work reliably even in areas without connectivity, auto-syncing data once the user is back online.
- Real-time updates and caching. Field updates should flow into back-office systems seamlessly through ETL processes, supporting near-real-time visibility.
- Rich digital records. Photos, notes, and documents attached at the point of capture provide visibility across the organization as well as compliance and reporting needs.
"30% reduction in project delivery time can be achieved by implementing digital field enablement."
- Gartner and Deloitte
2. Integrate seamlessly with utility systems
To fully leverage digital as-built capture, utilities must integrate core enterprise systems into a single application, enabling field teams to see the complete network and operational context.
For as-builts, the key systems to integrate include:
- GIS platforms (Esri ArcGIS, GE Smallworld)
- Desktop design tools (Hexagon Intergraph, ArcFM, Smallworld, Clevest, Lovion)
- ERP systems (ArcFM, Clevest, Epoch, LocusView)
- Online map services (Google, GIS web services)
- Reporting and other enterprise systems
The most successful integrations follow open, no-code principles, eliminating vendor lock-in and making it easier to scale and adapt the solution.
3. Align with real-world field and office workflows
A digital as-built solution must align with how teams actually work in both the field and the office. While specific workflows may vary across organizations, the overall process typically follows this structure:
For field users | For GIS techs |
See how to quickly perform redlines on a meter connection by using a tablet in the field instead of paper map markups. |
See how an office user can quickly access digital redlines that were performed in the field and then synced with the GIS. |
4. Define the correct KPIs
Each utility defines its own as-built key performance indicators (KPIs) to define success and understand where improvements need to occur. These key metrics include:
- Total time to complete new customer connections
- Percentage of scheduled man-hours to total man-hours
- Average cost per design
- Average time per design
- Number of truck rolls per design
By implementing the previous three steps, IQGeo can help electric utilities achieve their preferred KPIs. In fact, IQGeo’s customers have seen up to a 30% reduction in project delivery time through digital field enablement.
The future of as-built capture for electric utilities
Digital as-built capture is more than a technical upgrade or a change from standard processes. Implemented correctly, it’s a catalyst for smarter, faster, and safer grid operations. These best practices underpin the IQGeo's geospatial software, which unifies spatial awareness, field mobility, and workflow integration to support utility operations from initial design through final as-built. Download the best practice guide to explore the key insights in greater detail.
Interested in discussing a modern, digital as-built solution? Get in touch with our team today.
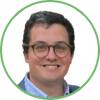
Sales Director - Utilities, IQGeo
Similar articles: